বিভিন্ন শিল্পে গ্রাইন্ডিং ডিস্ক একটি গুরুত্বপূর্ণ ভূমিকা পালন করে, যা উপকরণের আকৃতি এবং সমাপ্তি সহজতর করে। তবে, অন্যান্য যেকোনো সরঞ্জামের মতো, এগুলিও এমন সমস্যা থেকে মুক্ত নয় যা তাদের দক্ষতা এবং কর্মক্ষমতাকে ব্যাহত করতে পারে। এই নিবন্ধে, আমরা সাধারণ গ্রাইন্ডিং ডিস্ক সমস্যাগুলি অনুসন্ধান করব, তাদের মূল কারণগুলি অন্বেষণ করব এবং একটি নিরবচ্ছিন্ন কর্মপ্রবাহের জন্য কার্যকর সমাধান প্রদান করব।
ভূমিকা
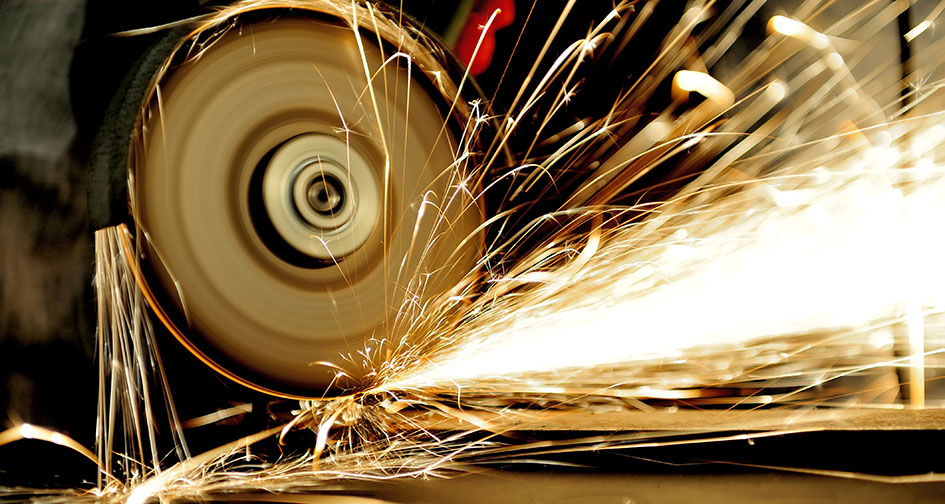
গ্রাইন্ডিং ডিস্ক বিভিন্ন শিল্পে একটি মৌলিক ভূমিকা পালন করে, যা উপাদান অপসারণ, আকৃতি এবং সমাপ্তি প্রক্রিয়ার জন্য অপরিহার্য হাতিয়ার হিসেবে কাজ করে। তাদের সংজ্ঞা, শিল্প জুড়ে গুরুত্ব এবং সাধারণ সমস্যাগুলি বোঝা তাদের ব্যবহার সর্বোত্তম করার জন্য এবং দক্ষ ক্রিয়াকলাপ নিশ্চিত করার জন্য অত্যন্ত গুরুত্বপূর্ণ।
ক. গ্রাইন্ডিং ডিস্কের সংজ্ঞা
গ্রাইন্ডিং ডিস্ক হল ঘষিয়া তুলিয়া ফেলিতে সক্ষম সরঞ্জাম যা যন্ত্র প্রক্রিয়ায় উপকরণের পৃষ্ঠতল কাটা, পিষে ফেলা বা পালিশ করার জন্য ব্যবহৃত হয়। এই ডিস্কগুলিতে সাধারণত ঘষিয়া তুলিয়া ফেলিতে সক্ষম কণা থাকে যা একটি ব্যাকিং উপাদানের সাথে সংযুক্ত থাকে, যা একটি ঘূর্ণায়মান সরঞ্জাম তৈরি করে যা অতিরিক্ত উপাদান অপসারণ করতে পারে, পৃষ্ঠতল মসৃণ করতে পারে বা প্রান্তগুলিকে তীক্ষ্ণ করতে পারে। এগুলি বিভিন্ন আকার এবং আকারে আসে, প্রতিটি নির্দিষ্ট অ্যাপ্লিকেশনের জন্য ডিজাইন করা হয়েছে।
খ. বিভিন্ন শিল্পে গুরুত্ব
ধাতব শিল্প:
ধাতব তৈরি এবং উৎপাদনে, ধাতব পৃষ্ঠতলের আকৃতি, ডিবারিং এবং সমাপ্তির জন্য গ্রাইন্ডিং ডিস্কগুলি অত্যন্ত গুরুত্বপূর্ণ। সুনির্দিষ্ট মাত্রা এবং পৃষ্ঠের গুণমান অর্জনের জন্য এগুলি সাধারণত অ্যাঙ্গেল গ্রাইন্ডারের সাথে ব্যবহৃত হয়।
নির্মাণ শিল্প:
নির্মাণ পেশাদাররা কংক্রিটের পৃষ্ঠ প্রস্তুতি, রুক্ষ প্রান্ত মসৃণ করা এবং পাথর ও কংক্রিটের মতো উপকরণের ত্রুটি দূর করার মতো কাজের জন্য গ্রাইন্ডিং ডিস্কের উপর নির্ভর করেন।
মোটরগাড়ি শিল্প:
মোটরগাড়ি খাতে গ্রাইন্ডিং ডিস্ক অপরিহার্য, যা বিভিন্ন সরঞ্জাম ধারালো করা থেকে শুরু করে ধাতব উপাদানের আকার পরিবর্তন এবং সমাপ্তি পর্যন্ত বিভিন্ন কাজে ব্যবহৃত হয়। এগুলি মোটরগাড়ির যন্ত্রাংশের নির্ভুলতা এবং গুণমানে অবদান রাখে।
কাঠের শিল্প:
কাঠের কারিগররা কাঠের পৃষ্ঠতলকে আকৃতি এবং মসৃণ করার জন্য গ্রাইন্ডিং ডিস্ক ব্যবহার করে। এই ডিস্কগুলি অতিরিক্ত উপাদান অপসারণ, আকার পরিমার্জন এবং আরও সমাপ্তির জন্য কাঠ প্রস্তুত করতে কার্যকর।
সাধারণ উৎপাদন:
গ্রাইন্ডিং ডিস্ক বিভিন্ন উৎপাদন প্রক্রিয়ায় প্রয়োগ করা হয় যেখানে সুনির্দিষ্ট উপাদান অপসারণের প্রয়োজন হয়, যা উচ্চ-মানের উপাদান উৎপাদনে অবদান রাখে।
গ. সাধারণ সমস্যাগুলি
ডিস্কের ক্ষয় এবং ঘর্ষণ:
ক্রমাগত ব্যবহারের ফলে গ্রাইন্ডিং ডিস্কের ক্ষয় এবং ঘর্ষণ হতে পারে, যা এর কর্মক্ষমতাকে প্রভাবিত করে। দক্ষতা বজায় রাখার জন্য নিয়মিত পরিদর্শন এবং প্রতিস্থাপন প্রয়োজন।
অতিরিক্ত গরম:
দীর্ঘক্ষণ ব্যবহারের সময় অতিরিক্ত ঘর্ষণ অতিরিক্ত গরম হতে পারে, যা ডিস্কের স্থায়িত্ব এবং সমাপ্ত পৃষ্ঠের গুণমানকে প্রভাবিত করে। সঠিক শীতলকরণ ব্যবস্থা এবং পর্যায়ক্রমিক বিরতি অপরিহার্য।
আটকে থাকা:
ডিস্ক গ্রাইন্ডিং করলে উপাদানের অবশিষ্টাংশ জমা হতে পারে, যার ফলে এর কার্যকারিতা হ্রাস পায়। নিয়মিত পরিষ্কার করা বা অ্যান্টি-ক্লগিং বৈশিষ্ট্যযুক্ত ডিস্ক নির্বাচন করা এই সমস্যা প্রতিরোধে সাহায্য করে।
কম্পন এবং টলমল:
ভারসাম্যহীনতা বা অসম ক্ষয়ের ফলে কম্পন বা টলমল হতে পারে, যা ফিনিশের মান এবং অপারেশনের নিরাপত্তা উভয়কেই প্রভাবিত করে। সঠিক ইনস্টলেশন এবং ভারসাম্য অত্যন্ত গুরুত্বপূর্ণ।
ভুল ডিস্ক নির্বাচন:
নির্দিষ্ট উপাদান বা ব্যবহারের জন্য ভুল ধরণের গ্রাইন্ডিং ডিস্ক নির্বাচন করলে অদক্ষতা এবং সম্ভাব্য ক্ষতি হতে পারে। উপাদানের সামঞ্জস্যের উপর ভিত্তি করে সঠিক নির্বাচন অপরিহার্য।
এই সরঞ্জামগুলির উপর নির্ভরশীল শিল্পগুলির জন্য গ্রাইন্ডিং ডিস্কের সংজ্ঞা, তাৎপর্য এবং সম্ভাব্য চ্যালেঞ্জগুলি বোঝা অপরিহার্য। সাধারণ সমস্যাগুলি সমাধান করে এবং সঠিক ব্যবহার নিশ্চিত করে, শিল্পগুলি তাদের নিজ নিজ প্রয়োগে গ্রাইন্ডিং ডিস্কের কার্যকারিতা সর্বাধিক করতে পারে।
গ্রাইন্ডিং ডিস্কের ক্ষয় এবং ছিঁড়ে যাওয়া
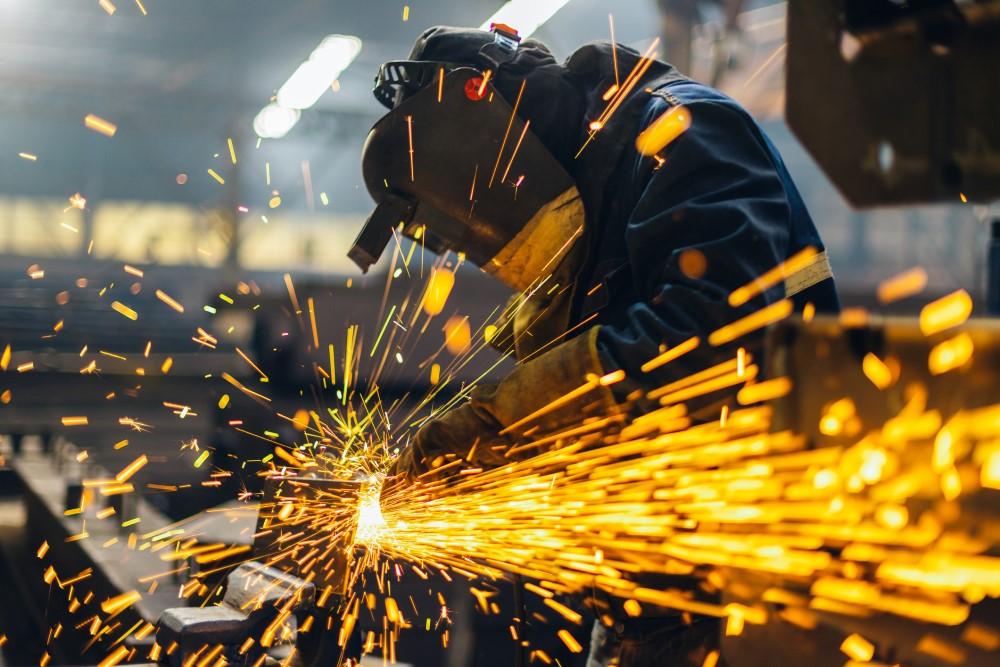
বিভিন্ন শিল্পে গ্রাইন্ডিং ডিস্ক হল অপরিহার্য হাতিয়ার, যা ধাতব তৈরি থেকে শুরু করে কংক্রিট পলিশিং পর্যন্ত বিভিন্ন কাজের জন্য প্রয়োজনীয় ঘর্ষণ প্রদান করে। গ্রাইন্ডিং ডিস্কের ক্ষয়ক্ষতির কারণগুলি বোঝা তাদের কর্মক্ষমতা সর্বোত্তম করার এবং সুরক্ষা নিশ্চিত করার জন্য অত্যন্ত গুরুত্বপূর্ণ।
উপাদানের কঠোরতা এবং গঠন:
কঠোরতার বৈচিত্র্য:গ্রাইন্ডিং ডিস্কের কঠোরতার মাত্রা বিভিন্ন ধরণের উপকরণের সাথে দেখা হয়। ধাতু এবং কংক্রিটের মতো ঘষিয়া তুলিয়া ফেলিতে সক্ষম উপকরণগুলির কঠোরতা উল্লেখযোগ্যভাবে ভিন্ন হতে পারে। শক্ত পদার্থের বিরুদ্ধে ক্রমাগত গ্রাইন্ডিং ক্ষয়কে ত্বরান্বিত করে।
উপাদান গঠন:গ্রাইন্ডিং করার সময় উপাদানটিতে ঘষিয়া তুলিয়া ফেলিতে সক্ষম উপাদানের উপস্থিতি গ্রাইন্ডিং ডিস্কের ক্ষয়ক্ষতির উপর প্রভাব ফেলতে পারে। ঘষিয়া তুলিয়া ফেলিতে সক্ষম কণা ডিস্কের ক্ষয়ক্ষতি ত্বরান্বিত করতে পারে।
গ্রাইন্ডিং চাপ এবং বল:
অতিরিক্ত চাপ:গ্রাইন্ডিং ডিস্কের উপর অতিরিক্ত চাপ প্রয়োগ করলে দ্রুত ক্ষয় হতে পারে। ডিস্কের উপর অপ্রয়োজনীয় চাপ এড়াতে নির্দিষ্ট প্রয়োগের জন্য প্রস্তাবিত চাপ ব্যবহার করা অপরিহার্য।
অপর্যাপ্ত বল: অন্যদিকে, অপর্যাপ্ত বল প্রয়োগের ফলে দীর্ঘক্ষণ ধরে ঘর্ষণ হতে পারে, অতিরিক্ত ঘর্ষণ এবং তাপ তৈরি হতে পারে, যা ক্ষয়ক্ষতির কারণ হতে পারে।
ডিস্কের গুণমান এবং রচনা:
ঘষিয়া তুলিয়া ফেলিতে সক্ষম উপাদানের গুণমান:গ্রাইন্ডিং ডিস্কে ব্যবহৃত ঘষিয়া তুলিয়া ফেলিতে সক্ষম উপাদানের গুণমান এর জীবনকালকে উল্লেখযোগ্যভাবে প্রভাবিত করে। উচ্চমানের ঘষিয়া তুলিয়া ফেলিতে সক্ষম উপকরণগুলি ক্ষয় প্রতিরোধ করে এবং দীর্ঘ সময় ধরে তীক্ষ্ণতা বজায় রাখে।
বন্ধনকারী এজেন্ট:যে বন্ধনকারী এজেন্ট ঘষিয়া তুলিয়া ফেলিতে সক্ষম কণাগুলিকে একত্রে ধরে রাখে, তা একটি গুরুত্বপূর্ণ ভূমিকা পালন করে। একটি সু-নকশিত বন্ধনকারী এজেন্ট ডিস্কের স্থায়িত্ব বাড়ায়।
কর্ম পরিবেশের শর্তাবলী:
তাপমাত্রা:গ্রাইন্ডিংয়ের সময় উৎপন্ন উচ্চ তাপমাত্রা ডিস্কের গঠনকে প্রভাবিত করতে পারে। অতিরিক্ত তাপ বন্ধনকারী এজেন্টকে দুর্বল করে এবং ক্ষয়কে ত্বরান্বিত করে।
আর্দ্রতা এবং দূষণকারী পদার্থ:কর্মক্ষেত্রে আর্দ্রতা বা দূষণকারী পদার্থের সংস্পর্শে গ্রাইন্ডিং ডিস্কের অখণ্ডতা প্রভাবিত করতে পারে, যার ফলে দ্রুত ক্ষয় হতে পারে।
অপারেটর কৌশল:
সঠিক কৌশল:অপারেটরের দক্ষতা এবং কৌশল অত্যন্ত গুরুত্বপূর্ণ। ভুল ব্যবহার, যেমন ভুল কোণে পিষে ফেলা বা অতিরিক্ত বল প্রয়োগ, অসম ক্ষয়ক্ষতিতে অবদান রাখতে পারে এবং ডিস্কের স্থায়িত্ব হ্রাস করতে পারে।
নিয়মিত পরিদর্শন:অপারেটরদের নিয়মিতভাবে গ্রাইন্ডিং ডিস্কটি পরিদর্শন করা উচিত যাতে কোনও ক্ষতি বা ক্ষয়ের লক্ষণ দেখা যায়। নির্দিষ্ট বিন্দুর বেশি ক্ষয় দেখা যাওয়া ডিস্কগুলি অবিলম্বে প্রতিস্থাপন করা উচিত।
ডিস্কের আকার এবং RPM সামঞ্জস্য:
সঠিক আকার নির্ধারণ:গ্রাইন্ডারের জন্য সঠিক ডিস্কের আকার ব্যবহার করা অত্যন্ত গুরুত্বপূর্ণ। ভুল আকারের ডিস্কগুলি অসমভাবে ক্ষয়প্রাপ্ত হতে পারে বা নিরাপত্তা ঝুঁকি তৈরি করতে পারে।
RPM সামঞ্জস্য:গ্রাইন্ডিং ডিস্কের জন্য প্রস্তাবিত প্রতি মিনিট ঘূর্ণন (RPM) মেনে চললে সর্বোত্তম কর্মক্ষমতা নিশ্চিত হয় এবং অকাল ক্ষয় রোধ করা যায়।
নিয়মিত রক্ষণাবেক্ষণ, প্রস্তাবিত অপারেটিং শর্তাবলী মেনে চলা এবং কাজের জন্য সঠিক গ্রাইন্ডিং ডিস্ক নির্বাচন করা ক্ষয়ক্ষতি কমানোর জন্য অপরিহার্য অনুশীলন। ক্ষয়ক্ষতিকে প্রভাবিতকারী কারণগুলি বোঝার মাধ্যমে, অপারেটররা গ্রাইন্ডিং ডিস্কের দীর্ঘায়ু এবং দক্ষতা বৃদ্ধি করতে পারে, যা নিরাপদ এবং আরও উৎপাদনশীল গ্রাইন্ডিং অপারেশনে অবদান রাখতে পারে।
অসম গ্রাইন্ডিং
অসম গ্রাইন্ডিং বলতে এমন একটি পরিস্থিতি বোঝায় যেখানে পৃষ্ঠটি মাটিতে স্থাপিত হওয়ার ফলে একটি সুসংগত এবং মসৃণ সমাপ্তি অর্জন করা যায় না। এই সমস্যাটি বিভিন্ন কারণে দেখা দিতে পারে এবং ওয়ার্কপিসের গুণমানকে প্রভাবিত করতে পারে। অসম গ্রাইন্ডিংয়ের জন্য অবদান রাখার সাধারণ কারণগুলি এবং সম্ভাব্য সমাধানগুলি এখানে দেওয়া হল:
ভুল গ্রাইন্ডিং হুইল নির্বাচন:
সমাধান:নিশ্চিত করুন যে গ্রাইন্ডিং হুইলটি গ্রাইন্ডিং করার জন্য উপযুক্ত। বিভিন্ন উপকরণের জন্য নির্দিষ্ট ঘষিয়া তুলিয়া ফেলিতে সক্ষম বৈশিষ্ট্য প্রয়োজন। প্রয়োগের জন্য সঠিক চাকার ধরণ, গ্রিটের আকার এবং বন্ধন বেছে নিন।
অনুপযুক্ত চাকা ড্রেসিং:
কারণ:একটি গ্রাইন্ডিং হুইল যা সঠিকভাবে পরিধান করা হয়নি, তার ফলে অসম ক্ষয় এবং অকার্যকর কাটা হতে পারে।
সমাধান:নিয়মিতভাবে গ্রাইন্ডিং হুইলটি সাজিয়ে দিন যাতে এর আকৃতি বজায় থাকে এবং জমে থাকা ধ্বংসাবশেষ অপসারণ করা যায়। সঠিক সাজসজ্জা একটি সুসংগত কাটিয়া পৃষ্ঠ নিশ্চিত করে।
অপর্যাপ্ত গ্রাইন্ডিং ফ্লুইড বা কুল্যান্ট:
কারণ:গ্রাইন্ডিং তরলের অপর্যাপ্ত বা অনুপযুক্ত ব্যবহারের ফলে ঘর্ষণ এবং তাপ বৃদ্ধি পেতে পারে, যার ফলে অসম গ্রাইন্ডিং হতে পারে।
সমাধান:তাপ অপচয় করতে এবং ঘর্ষণ কমাতে উপযুক্ত গ্রাইন্ডিং তরল বা কুল্যান্ট ব্যবহার করুন। অভিন্ন ফলাফল অর্জনের জন্য সঠিক শীতলকরণ অপরিহার্য।
ভুল গ্রাইন্ডিং প্যারামিটার:
কারণ:অতিরিক্ত গতি, ফিড রেট, বা কাটার গভীরতার মতো ভুল গ্রাইন্ডিং প্যারামিটার ব্যবহার করলে অসম গ্রাইন্ডিং হতে পারে।
সমাধান:উপাদান এবং প্রয়োগের প্রয়োজনীয়তা অনুসারে গ্রাইন্ডিং প্যারামিটারগুলি সামঞ্জস্য করুন। সর্বোত্তম সেটিংসের জন্য প্রস্তুতকারকের সুপারিশগুলি পড়ুন।
জীর্ণ নাকাল চাকা:
কারণ:একটি জীর্ণ গ্রাইন্ডিং হুইল একটি সামঞ্জস্যপূর্ণ কাটিয়া পৃষ্ঠ প্রদান নাও করতে পারে, যার ফলে অসম গ্রাইন্ডিং হয়।
সমাধান:গ্রাইন্ডিং হুইলটি ব্যবহারের শেষ সময়সীমা পার হয়ে গেলে প্রতিস্থাপন করুন। ক্ষয়ের লক্ষণগুলির জন্য নিয়মিত চাকাটি পরীক্ষা করুন।
অসম চাপ বা ফিড রেট:
কারণ:গ্রাইন্ডিংয়ের সময় অসম চাপ বা অসঙ্গত ফিডের হার অনিয়মিত উপাদান অপসারণের কারণ হতে পারে।
সমাধান:ওয়ার্কপিস জুড়ে সমান চাপ প্রয়োগ করুন এবং একটি সুসংগত ফিড রেট বজায় রাখুন। অপারেটরের দক্ষতা এবং বিস্তারিত মনোযোগ অত্যন্ত গুরুত্বপূর্ণ।
মেশিনের সমস্যা:
কারণ:গ্রাইন্ডিং মেশিনের যান্ত্রিক সমস্যা, যেমন ভুল সারিবদ্ধতা বা স্পিন্ডেলের সমস্যা, অসম গ্রাইন্ডিংয়ের কারণ হতে পারে।
সমাধান:গ্রাইন্ডিং মেশিনের নিয়মিত রক্ষণাবেক্ষণ পরীক্ষা করুন। সঠিক কার্যকারিতা নিশ্চিত করতে যেকোনো যান্ত্রিক সমস্যা দ্রুত সমাধান করুন।
ওয়ার্কপিস ফিক্সচারিং:
কারণ:খারাপভাবে সংযুক্ত বা ভুলভাবে সারিবদ্ধ ওয়ার্কপিসগুলি অসমভাবে নাকাল হতে পারে।
সমাধান:ওয়ার্কপিসের সঠিক ফিক্সচারিং এবং সারিবদ্ধকরণ নিশ্চিত করুন। গ্রাইন্ডিং প্রক্রিয়ার সময় নড়াচড়া রোধ করার জন্য এটি শক্তভাবে সুরক্ষিত করুন।
অসম গ্রাইন্ডিং মোকাবেলার জন্য সঠিক সরঞ্জাম সেটআপ, সঠিক অপারেটিং প্যারামিটার এবং নিয়মিত রক্ষণাবেক্ষণ অনুশীলনের সমন্বয় প্রয়োজন। গ্রাইন্ডিং অ্যাপ্লিকেশনগুলিতে উচ্চ-মানের এবং ধারাবাহিক ফলাফল অর্জনের জন্য অপারেটরদের তাৎক্ষণিকভাবে সমস্যাগুলি সনাক্ত এবং সংশোধন করার জন্য প্রশিক্ষণ দেওয়া উচিত। নিয়মিত পরিদর্শন এবং সর্বোত্তম অনুশীলনগুলি মেনে চলা গ্রাইন্ডিং প্রক্রিয়া চলাকালীন দক্ষ এবং অভিন্ন উপাদান অপসারণে অবদান রাখে।
অতিরিক্ত গরমের সমস্যা
গ্রাইন্ডিং করার সময় অতিরিক্ত গরম হওয়া একটি সাধারণ সমস্যা যা গ্রাইন্ডিং হুইল এবং ওয়ার্কপিস উভয়েরই কর্মক্ষমতাকে প্রভাবিত করতে পারে। অতিরিক্ত তাপ বিভিন্ন সমস্যার সৃষ্টি করতে পারে, যার মধ্যে রয়েছে চাকার আয়ু হ্রাস, ওয়ার্কপিসের তাপীয় ক্ষতি এবং সামগ্রিকভাবে গ্রাইন্ডিং দক্ষতা হ্রাস। অতিরিক্ত গরমের সমস্যা সমাধানের সম্ভাব্য কারণ এবং সমাধান এখানে দেওয়া হল:
ভুল গ্রাইন্ডিং প্যারামিটার:
কারণ:অনুপযুক্ত গ্রাইন্ডিং প্যারামিটার ব্যবহার করা, যেমন অতিরিক্ত গতি, ফিড রেট, বা কাটার গভীরতা, অতিরিক্ত তাপ উৎপন্ন করতে পারে।
সমাধান:প্রস্তাবিত সীমার মধ্যে গ্রাইন্ডিং প্যারামিটারগুলি সামঞ্জস্য করুন। গ্রাইন্ডিং করা উপাদানের উপর ভিত্তি করে সর্বোত্তম সেটিংসের জন্য প্রস্তুতকারকের নির্দেশিকাগুলি দেখুন।
অপর্যাপ্ত শীতলকরণ বা তৈলাক্তকরণ:
কারণ:কুল্যান্ট বা গ্রাইন্ডিং তরলের অপর্যাপ্ত ব্যবহার ঘর্ষণ এবং তাপ বৃদ্ধি করতে পারে।
সমাধান:গ্রাইন্ডিং প্রক্রিয়ার সময় পর্যাপ্ত পরিমাণে কুল্যান্ট বা লুব্রিকেন্ট সরবরাহ নিশ্চিত করুন। সঠিক ঠান্ডা তাপ অপচয় করতে সাহায্য করে এবং তাপীয় ক্ষতি প্রতিরোধ করে।
ভুল চাকা নির্বাচন:
কারণ:গ্রাইন্ডিং হুইল নির্বাচন করলে উপাদানটি গ্রাইন্ডিংয়ের জন্য অনুপযুক্ত স্পেসিফিকেশনের কারণে অতিরিক্ত গরম হতে পারে।
সমাধান:নির্দিষ্ট ব্যবহারের জন্য সঠিক ঘষিয়া তুলিয়া ফেলিতে সক্ষম ধরণ, গ্রিটের আকার এবং বন্ধন সহ একটি গ্রাইন্ডিং হুইল নির্বাচন করুন। উপাদানের সাথে চাকা মেলালে তাপ উৎপাদন কম হয়।
ওয়ার্কপিস উপাদানের সমস্যা:
কারণ:কিছু উপকরণ, বিশেষ করে যাদের তাপ পরিবাহিতা কম, সেগুলো গ্রাইন্ডিংয়ের সময় অতিরিক্ত গরম হওয়ার ঝুঁকি বেশি থাকে।
সমাধান:কম তাপ পরিবাহিতা সম্পন্ন উপকরণের জন্য গ্রাইন্ডিং প্যারামিটারগুলি সামঞ্জস্য করুন। তাপ-সংবেদনশীল উপকরণের জন্য ডিজাইন করা একটি বিশেষ গ্রাইন্ডিং হুইল ব্যবহার করার কথা বিবেচনা করুন।
চাকা ড্রেসিং সমস্যা:
কারণ:গ্রাইন্ডিং হুইলের অনিয়ম বা অনুপযুক্ত ড্রেসিংয়ের ফলে অসম যোগাযোগ এবং তাপ জমা হতে পারে।
সমাধান:নিয়মিতভাবে গ্রাইন্ডিং হুইলটি সাজিয়ে রাখুন যাতে এর আকৃতি বজায় থাকে এবং যেকোনো গ্লাসিং বা জমে থাকা ধ্বংসাবশেষ অপসারণ করা যায়। সঠিকভাবে সাজানো চাকাগুলি ধারাবাহিক গ্রাইন্ডিং কর্মক্ষমতা নিশ্চিত করে।
অপর্যাপ্ত মেশিন রক্ষণাবেক্ষণ:
কারণ:খারাপভাবে রক্ষণাবেক্ষণ করা গ্রাইন্ডিং মেশিনগুলি অতিরিক্ত গরমের সমস্যা তৈরি করতে পারে।
সমাধান:গ্রাইন্ডিং মেশিনের নিয়মিত রক্ষণাবেক্ষণ করুন, যার মধ্যে রয়েছে কুল্যান্ট সিস্টেম পরীক্ষা করা, চাকার ড্রেসিং সরঞ্জাম পরিদর্শন করা এবং সঠিক সারিবদ্ধকরণ নিশ্চিত করা। যেকোনো যান্ত্রিক সমস্যা দ্রুত সমাধান করুন।
অপর্যাপ্ত চাকা কুল্যান্ট প্রবাহ:
কারণ:গ্রাইন্ডিং জোনে অপর্যাপ্ত কুল্যান্ট প্রবাহের ফলে তাপ অপচয় হ্রাস পেতে পারে।
সমাধান:কুল্যান্ট ডেলিভারি সিস্টেমটি পরীক্ষা করুন এবং অপ্টিমাইজ করুন। নিশ্চিত করুন যে কুল্যান্ট কার্যকরভাবে গ্রাইন্ডিং জোনে পৌঁছায় যাতে শীতলকরণের দক্ষতা বজায় থাকে।
অতিরিক্ত গ্রাইন্ডিং সময়:
কারণ:বিরতি ছাড়াই দীর্ঘক্ষণ ধরে গ্রাইন্ডিং সেশন তাপ জমাতে অবদান রাখতে পারে।
সমাধান:মাঝেমধ্যে গ্রাইন্ডিং প্রয়োগ করুন এবং অতিরিক্ত তাপ জমা হওয়া রোধ করার জন্য বিরতি দিন। এই পদ্ধতিটি বিশেষ করে বড় বা চ্যালেঞ্জিং গ্রাইন্ডিং কাজের জন্য গুরুত্বপূর্ণ।
গ্রাইন্ডিংয়ে অতিরিক্ত গরমের সমস্যা সমাধানের জন্য সঠিক সরঞ্জাম সেটআপ, উপযুক্ত গ্রাইন্ডিং প্যারামিটার এবং নিয়মিত রক্ষণাবেক্ষণ অনুশীলনের মাধ্যমে একটি বিস্তৃত পদ্ধতির প্রয়োজন। সর্বোত্তম কর্মক্ষমতা, বর্ধিত সরঞ্জামের জীবনকাল এবং উচ্চ-মানের ফলাফল নিশ্চিত করতে অপারেটরদের গ্রাইন্ডিং প্রক্রিয়া চলাকালীন তাপ উৎপাদন পর্যবেক্ষণ এবং নিয়ন্ত্রণ করা উচিত।
কম্পন সম্পর্কিত উদ্বেগ
গ্রাইন্ডিং অপারেশনের সময় অতিরিক্ত কম্পনের ফলে বিভিন্ন সমস্যা দেখা দিতে পারে, যার মধ্যে রয়েছে পৃষ্ঠের গুণমান হ্রাস, সরঞ্জামের ক্ষয় বৃদ্ধি এবং গ্রাইন্ডিং মেশিনের সম্ভাব্য ক্ষতি। সুনির্দিষ্ট এবং দক্ষ গ্রাইন্ডিং প্রক্রিয়া অর্জনের জন্য কম্পনের উদ্বেগগুলি সমাধান করা অত্যন্ত গুরুত্বপূর্ণ। কম্পনের সমস্যাগুলি প্রশমিত করার সম্ভাব্য কারণ এবং সমাধানগুলি এখানে দেওয়া হল:
অসম চাকার ক্ষয়:
কারণ:গ্রাইন্ডিং হুইলে অনিয়মিত ক্ষয়ক্ষতির ফলে ওয়ার্কপিসের সাথে অসম যোগাযোগ হতে পারে, যার ফলে কম্পন দেখা দিতে পারে।
সমাধান:নিয়মিতভাবে গ্রাইন্ডিং হুইলটি পরিদর্শন করুন এবং একটি সুসংগত এবং সমতল পৃষ্ঠ বজায় রাখার জন্য এটিকে সাজিয়ে তুলুন। সঠিক চাকার রক্ষণাবেক্ষণ কম্পন কমাতে সাহায্য করে।
ভারসাম্যহীন গ্রাইন্ডিং হুইল:
কারণ:গ্রাইন্ডিং হুইলে ভারসাম্যহীনতা, তা অসম পরিধানের কারণে হোক বা উৎপাদন ত্রুটির কারণে হোক, কম্পনের কারণ হতে পারে।
সমাধান:হুইল ব্যালেন্সার ব্যবহার করে গ্রাইন্ডিং হুইলটি ভারসাম্যপূর্ণ করুন। ভারসাম্য বজায় রাখার ফলে ওজনের সমান বন্টন নিশ্চিত হয় এবং অপারেশনের সময় কম্পন হ্রাস পায়।
অপর্যাপ্ত মেশিন ক্যালিব্রেশন:
কারণ:চাকার স্পিন্ডেল বা ওয়ার্কটেবলের মতো মেশিনের যন্ত্রাংশের দুর্বল ক্রমাঙ্কন বা ভুল সারিবদ্ধকরণ কম্পনের কারণ হতে পারে।
সমাধান:সঠিক কার্যকারিতা নিশ্চিত করতে নিয়মিতভাবে মেশিনের উপাদানগুলি ক্যালিব্রেট এবং সারিবদ্ধ করুন। মেশিন সেটআপ এবং সারিবদ্ধকরণের জন্য প্রস্তুতকারকের নির্দেশিকা অনুসরণ করুন।
ওয়ার্কপিস ভারসাম্যহীনতা:
কারণ:একটি অসম বা অনুপযুক্তভাবে সুরক্ষিত ওয়ার্কপিস ভারসাম্যহীনতা তৈরি করতে পারে এবং কম্পন সৃষ্টি করতে পারে।
সমাধান:ওয়ার্কপিসটি সঠিকভাবে সুরক্ষিত করুন, নিশ্চিত করুন যে এটি সমানভাবে অবস্থিত এবং ক্ল্যাম্প করা আছে। গ্রাইন্ডিং প্রক্রিয়া শুরু করার আগে যেকোনো ভারসাম্যহীনতার সমস্যা সমাধান করুন।
ভুল চাকা নির্বাচন:
কারণ:অনুপযুক্ত স্পেসিফিকেশন সহ গ্রাইন্ডিং হুইল ব্যবহার করলে কম্পন হতে পারে।
সমাধান:সঠিক ঘষিয়া তুলিয়া ফেলিতে সক্ষম ধরণ, গ্রিটের আকার এবং গ্রাইন্ডিং উপাদানের জন্য বন্ধন সহ একটি গ্রাইন্ডিং হুইল নির্বাচন করুন। অ্যাপ্লিকেশনের সাথে চাকাটি মেলালে কম্পন কম হয়।
মেশিনের ক্ষয়ক্ষতি:
কারণ:জীর্ণ বা ক্ষতিগ্রস্ত মেশিনের উপাদান, যেমন বিয়ারিং বা স্পিন্ডেল, কম্পনে অবদান রাখতে পারে।
সমাধান:নিয়মিতভাবে মেশিনের জীর্ণ অংশগুলি পরিদর্শন এবং প্রতিস্থাপন করুন। সঠিক রক্ষণাবেক্ষণ অতিরিক্ত কম্পন প্রতিরোধ করতে সাহায্য করে এবং গ্রাইন্ডিং মেশিনের আয়ু বাড়ায়।
অপর্যাপ্ত কুল্যান্ট প্রবাহ:
কারণ:গ্রাইন্ডিং জোনে অপর্যাপ্ত কুল্যান্ট প্রবাহের ফলে তাপ জমা এবং কম্পন হতে পারে।
সমাধান:সঠিক শীতলতা নিশ্চিত করতে কুল্যান্ট ডেলিভারি সিস্টেমটি অপ্টিমাইজ করুন। কার্যকর শীতলতা তাপীয় প্রসারণ এবং সংকোচনের ঝুঁকি হ্রাস করে, যা কম্পনের কারণ হতে পারে।
টুল হোল্ডার সমস্যা:
কারণ:টুল হোল্ডার বা স্পিন্ডল ইন্টারফেসের সমস্যা কম্পনের কারণ হতে পারে।
সমাধান:নিশ্চিত করুন যে টুল হোল্ডারটি নিরাপদে মাউন্ট করা আছে এবং স্পিন্ডেলের সাথে সঠিকভাবে সারিবদ্ধ। কম্পন কমাতে উচ্চমানের এবং সঠিকভাবে রক্ষণাবেক্ষণ করা টুল হোল্ডার ব্যবহার করুন।
মেশিন ফাউন্ডেশন:
কারণ:দুর্বল মেশিনের ভিত্তি বা অপর্যাপ্ত সমর্থন কম্পনকে বাড়িয়ে তুলতে পারে।
সমাধান:নিশ্চিত করুন যে গ্রাইন্ডিং মেশিনটি একটি স্থিতিশীল এবং সঠিকভাবে ডিজাইন করা ভিত্তির উপর ইনস্টল করা আছে। মেশিনে প্রেরিত কম্পন কমাতে যেকোনো কাঠামোগত সমস্যা সমাধান করুন।
গ্রাইন্ডিংয়ে কম্পনের সমস্যাগুলি কার্যকরভাবে মোকাবেলা করার জন্য সঠিক মেশিন রক্ষণাবেক্ষণ, চাকা নির্বাচন এবং ওয়ার্কপিস হ্যান্ডলিং এর সমন্বয় প্রয়োজন। অপারেটরদের নিয়মিত পরিদর্শন এবং রক্ষণাবেক্ষণ অনুশীলনগুলি বাস্তবায়ন করা উচিত যাতে সমস্যাগুলি দ্রুত সনাক্ত করা যায় এবং সমাধান করা যায়, যার ফলে গ্রাইন্ডিং কর্মক্ষমতা এবং গুণমান উন্নত হয়।
গ্রাইন্ডিংয়ে লোডিং সমস্যা
গ্রাইন্ডিং-এ লোডিং বলতে এমন একটি ঘটনাকে বোঝায় যেখানে গ্রাইন্ডিং হুইলের ঘষিয়া তুলিয়া ফেলা দানার মধ্যবর্তী স্থানগুলি মাটিতে থাকা উপাদান দিয়ে পূর্ণ হয়ে যায়, যার ফলে কাটার ক্রিয়া হ্রাস পায় এবং ঘর্ষণ বৃদ্ধি পায়। লোডিং গ্রাইন্ডিং প্রক্রিয়ার দক্ষতা এবং গুণমানের উপর নেতিবাচক প্রভাব ফেলতে পারে। লোডিং সমস্যা সমাধানের সম্ভাব্য কারণ এবং সমাধান এখানে দেওয়া হল:
নরম ওয়ার্কপিস উপাদান:
কারণ:নরম উপকরণ পিষে ফেলার ফলে ঘষিয়া তুলিয়া ফেলিতে সক্ষম দানা দ্রুত আটকে যেতে পারে।
সমাধান:নরম উপকরণের উপর কাজ করার সময় মোটা গ্রিট এবং খোলা কাঠামোর গ্রাইন্ডিং হুইল ব্যবহার করুন। এটি দ্রুত লোডিং প্রতিরোধ করতে সাহায্য করে এবং কার্যকরভাবে চিপ অপসারণের সুযোগ দেয়।
উপাদান দূষণ:
কারণ:ওয়ার্কপিস উপাদানে উপস্থিত দূষণকারী পদার্থ, যেমন তেল, গ্রীস, বা কুল্যান্টের অবশিষ্টাংশ, লোডিংয়ে অবদান রাখতে পারে।
সমাধান:দূষিত পদার্থ অপসারণের জন্য গ্রাইন্ডিংয়ের আগে ওয়ার্কপিসটি সঠিকভাবে পরিষ্কার করুন। লোডিং কমাতে উপযুক্ত কাটিং তরল বা কুল্যান্ট ব্যবহার করুন।
ভুল কুল্যান্ট প্রয়োগ:
কারণ:কুল্যান্টের অপর্যাপ্ত বা অনুপযুক্ত প্রয়োগের ফলে অপর্যাপ্ত তৈলাক্তকরণ এবং শীতলকরণ হতে পারে, যার ফলে লোডিং হতে পারে।
সমাধান:কুল্যান্ট প্রবাহ এবং ঘনত্বকে সর্বোত্তম করুন। নিশ্চিত করুন যে কুল্যান্ট কার্যকরভাবে গ্রাইন্ডিং জোনে পৌঁছায় যাতে প্রক্রিয়াটি লুব্রিকেট এবং ঠান্ডা হয়, লোডিং প্রতিরোধ করে।
অপর্যাপ্ত চাকার তীক্ষ্ণতা:
কারণ:নিস্তেজ বা জীর্ণ গ্রাইন্ডিং চাকাগুলি তাদের কাটার দক্ষতা হারানোর কারণে লোড হওয়ার ঝুঁকি বেশি থাকে।
সমাধান:নিয়মিতভাবে গ্রাইন্ডিং হুইলটি পরিষ্কার করুন এবং ধারালো করুন যাতে এর তীক্ষ্ণতা বজায় থাকে। তাজা ঘষিয়া তুলিয়া ফেলিতে সক্ষম দানাগুলি উন্মুক্ত করতে এবং কাটার ক্রিয়া উন্নত করতে একটি হুইল ড্রেসার ব্যবহার করুন।
কম চাকার গতি:
কারণ:কম গতিতে গ্রাইন্ডিং হুইল চালানোর ফলে চিপস বের করার জন্য পর্যাপ্ত কেন্দ্রাতিগ বল নাও থাকতে পারে, যার ফলে লোডিং হতে পারে।
সমাধান:নির্দিষ্ট চাকা এবং ওয়ার্কপিস সংমিশ্রণের জন্য প্রস্তাবিত গতিতে গ্রাইন্ডিং মেশিনটি কাজ করছে কিনা তা নিশ্চিত করুন। উচ্চ গতি চিপ অপসারণে আরও ভালভাবে সাহায্য করতে পারে।
অতিরিক্ত চাপ:
কারণ:গ্রাইন্ডিংয়ের সময় অত্যধিক চাপ প্রয়োগ করলে উপাদানটি চাকার মধ্যে জোর করে ঢুকে যেতে পারে, যার ফলে লোডিং হতে পারে।
সমাধান:মাঝারি এবং সামঞ্জস্যপূর্ণ গ্রাইন্ডিং চাপ ব্যবহার করুন। অতিরিক্ত চাপ ছাড়াই চাকাটি দক্ষতার সাথে কাটার জন্য ফিড রেট সামঞ্জস্য করুন যা লোডিংয়ে পরিণত হয়।
ভুল চাকার স্পেসিফিকেশন:
কারণ:গ্রাইন্ডিং হুইল ব্যবহার করলে, উপাদানটি গ্রাইন্ড করার জন্য ভুল স্পেসিফিকেশন ব্যবহার করলে লোডিং হতে পারে।
সমাধান:নির্দিষ্ট ব্যবহারের জন্য উপযুক্ত ঘষিয়া তুলিয়া ফেলিতে সক্ষম ধরণ, গ্রিটের আকার এবং বন্ধন সহ একটি গ্রাইন্ডিং হুইল নির্বাচন করুন। উপাদানের সাথে চাকাটি মেলালে লোডিং প্রতিরোধ করা যায়।
অপর্যাপ্ত কুল্যান্ট পরিষ্কার:
কারণ:দূষিত বা পুরাতন কুল্যান্ট লোডিং সমস্যার কারণ হতে পারে।
সমাধান:দূষণকারী পদার্থ জমা হওয়া রোধ করতে নিয়মিত কুল্যান্ট পরিষ্কার করুন এবং প্রতিস্থাপন করুন। তাজা এবং পরিষ্কার কুল্যান্ট লুব্রিকেশন এবং শীতলতা বৃদ্ধি করে, লোড হওয়ার সম্ভাবনা হ্রাস করে।
অনুপযুক্ত ড্রেসিং কৌশল:
কারণ:গ্রাইন্ডিং হুইলের ভুল ড্রেসিংয়ের ফলে অনিয়ম এবং লোডিং হতে পারে।
সমাধান:উপযুক্ত ড্রেসিং টুল ব্যবহার করে চাকাটি সঠিকভাবে সাজান। লোডিং রোধ করার জন্য চাকার প্রোফাইলটি সামঞ্জস্যপূর্ণ এবং অনিয়মমুক্ত রয়েছে তা নিশ্চিত করুন।
লোডিং সমস্যাগুলি কার্যকরভাবে সমাধানের জন্য সঠিক চাকা নির্বাচন, মেশিন সেটআপ এবং রক্ষণাবেক্ষণ অনুশীলনের সমন্বয় জড়িত। অপারেটরদের সুপারিশকৃত পদ্ধতিগুলি অনুসরণ করা উচিত, উপযুক্ত গ্রাইন্ডিং প্যারামিটার ব্যবহার করা উচিত এবং লোডিং কমাতে এবং গ্রাইন্ডিং কর্মক্ষমতা সর্বোত্তম করার জন্য নিয়মিত চাকা ড্রেসিং প্রয়োগ করা উচিত।
বিভিন্ন ধাতব কাজ এবং তৈরির কাজে সর্বোত্তম ফলাফল অর্জনের জন্য সঠিক গ্রাইন্ডিং ডিস্ক নির্বাচন করা অত্যন্ত গুরুত্বপূর্ণ। নির্বাচনটি নির্ভর করে কোন উপাদানের উপর কাজ করা হচ্ছে, কাঙ্ক্ষিত ফিনিশিং এবং কোন ধরণের গ্রাইন্ডার ব্যবহার করা হচ্ছে তার উপর।
সঠিক গ্রাইন্ডিং ডিস্ক নির্বাচন করা
উপাদানের সামঞ্জস্য:
লৌহঘটিত ধাতু (ইস্পাত, লোহা):লৌহঘটিত ধাতুর জন্য বিশেষভাবে ডিজাইন করা গ্রাইন্ডিং ডিস্ক ব্যবহার করুন। এই ডিস্কগুলিতে প্রায়শই ইস্পাতের কঠোরতার জন্য উপযুক্ত ঘষিয়া তুলিয়া ফেলিতে সক্ষম পদার্থ থাকে এবং লোড হওয়ার সম্ভাবনা কম থাকে।
লৌহঘটিত ধাতু (অ্যালুমিনিয়াম, পিতল):ধাতু আটকে যাওয়া রোধ করার জন্য নরম ধাতুর জন্য উপযুক্ত ঘষিয়া তুলিয়া ফেলিতে সক্ষম ডিস্ক বেছে নিন। অ্যালুমিনিয়াম অক্সাইড বা সিলিকন কার্বাইড ডিস্ক সাধারণ পছন্দ।
ঘষিয়া তুলিয়া ফেলিতে সক্ষম উপাদান:
অ্যালুমিনিয়াম অক্সাইড:লৌহঘটিত ধাতুতে সাধারণ উদ্দেশ্যে পিষে ফেলার জন্য উপযুক্ত। এটি টেকসই এবং বহুমুখী।
জিরকোনিয়া অ্যালুমিনা:উচ্চতর কাটিংয়ের দক্ষতা এবং দীর্ঘায়ু প্রদান করে, যা এটিকে লৌহঘটিত এবং অ লৌহঘটিত ধাতুতে আক্রমণাত্মক গ্রাইন্ডিংয়ের জন্য উপযুক্ত করে তোলে।
সিলিকন কার্বাইড:অ লৌহঘটিত ধাতু এবং পাথর পিষে ফেলার জন্য আদর্শ। এটি অ্যালুমিনিয়াম অক্সাইডের তুলনায় ধারালো কিন্তু কম টেকসই।
গ্রিট আকার:
মোটা গ্রিট (২৪-৩৬):দ্রুত স্টক অপসারণ এবং ভারী-শুল্ক গ্রাইন্ডিং।
মাঝারি গ্রিট (৪০-৬০):স্টক অপসারণ এবং পৃষ্ঠ সমাপ্তির ভারসাম্য বজায় রাখে।
ফাইন গ্রিট (৮০-১২০):পৃষ্ঠ প্রস্তুতি এবং হালকা গ্রাইন্ডিংয়ের জন্য উপযুক্ত একটি মসৃণ ফিনিশ প্রদান করে।
চাকার ধরণ:
টাইপ ২৭ (বিষণ্ণতা কেন্দ্র):সমতল পৃষ্ঠ সহ স্ট্যান্ডার্ড গ্রাইন্ডিং ডিস্ক, পৃষ্ঠ গ্রাইন্ডিং এবং প্রান্ত কাজের জন্য আদর্শ।
টাইপ ২৯ (শঙ্কুযুক্ত):আক্রমণাত্মক স্টক অপসারণ এবং আরও ভাল পৃষ্ঠ মিশ্রণের জন্য কোণযুক্ত নকশা।
টাইপ ১ (সোজা):কাট-অফ অ্যাপ্লিকেশনের জন্য ব্যবহৃত হয়। এটি সঠিক কাটার জন্য একটি পাতলা প্রোফাইল প্রদান করে।
আবেদন:
নাকাল:উপাদান অপসারণ এবং আকার দেওয়ার জন্য স্ট্যান্ডার্ড গ্রাইন্ডিং ডিস্ক।
কাটা:ধাতু কাটার জন্য কাট-অফ চাকা ব্যবহার করুন, যা একটি সোজা এবং পরিষ্কার প্রান্ত প্রদান করে।
ফ্ল্যাপ ডিস্ক:গ্রাইন্ডিং এবং ফিনিশিং একসাথে একত্রিত করুন। পৃষ্ঠতল মিশ্রিত এবং মসৃণ করার জন্য উপযুক্ত।
গ্রাইন্ডারের সাথে সামঞ্জস্য:
গ্রাইন্ডিং ডিস্কটি ব্যবহৃত গ্রাইন্ডারের ধরণ এবং গতির সাথে সামঞ্জস্যপূর্ণ কিনা তা নিশ্চিত করুন। ডিস্কের সর্বোচ্চ RPM (প্রতি মিনিটে বিপ্লব) এর জন্য প্রস্তুতকারকের সুপারিশগুলি পরীক্ষা করুন।
কাজের নির্দিষ্টতা:
ভারী স্টক অপসারণ:কার্যকরভাবে উপাদান অপসারণের জন্য একটি মোটা গ্রিট এবং একটি টাইপ 27 বা টাইপ 29 ডিস্ক বেছে নিন।
সারফেস ফিনিশিং:মসৃণ ফিনিশের জন্য ফ্ল্যাপ ডিস্ক সহ মাঝারি থেকে সূক্ষ্ম গ্রিট বেছে নিন।
নিরাপত্তা বিবেচ্য বিষয়:
সুরক্ষা নির্দেশিকা অনুসরণ করুন, যার মধ্যে রয়েছে উপযুক্ত ব্যক্তিগত সুরক্ষামূলক সরঞ্জাম (PPE) যেমন সুরক্ষা চশমা এবং গ্লাভস পরা।
অতিরিক্ত স্থায়িত্ব এবং সুরক্ষার জন্য রিইনফোর্সড ডিস্ক বেছে নিন।
ব্র্যান্ড এবং মান:
গুণমান এবং ধারাবাহিকতার জন্য পরিচিত নামী ব্র্যান্ডের ডিস্কগুলি নির্বাচন করুন। উচ্চমানের ডিস্কগুলি আরও ভাল কর্মক্ষমতা এবং স্থায়িত্ব প্রদান করে।
খরচ বিবেচনা:
গ্রাইন্ডিং ডিস্কের প্রত্যাশিত জীবনকাল এবং কর্মক্ষমতার সাথে প্রাথমিক খরচের ভারসাম্য বজায় রাখুন। উচ্চমানের ডিস্কের প্রাথমিক খরচ বেশি হতে পারে তবে সময়ের সাথে সাথে এটি আরও ভাল মূল্য প্রদান করতে পারে।
এই বিষয়গুলি বিবেচনা করে, অপারেটররা তাদের নির্দিষ্ট অ্যাপ্লিকেশনের জন্য সঠিক গ্রাইন্ডিং ডিস্ক বেছে নিতে পারে, দক্ষতা, নিরাপত্তা এবং সর্বোত্তম ফলাফল নিশ্চিত করে।
উপসংহার
পরিশেষে, উপযুক্ত গ্রাইন্ডিং ডিস্ক নির্বাচন করা সফল ধাতব কাজ এবং তৈরির ফলাফল অর্জনের একটি গুরুত্বপূর্ণ দিক। পছন্দটি বিভিন্ন বিষয়ের উপর নির্ভর করে যেমন কাজ করা উপাদান, পছন্দসই ফিনিশ এবং ব্যবহৃত গ্রাইন্ডারের ধরণ। উপাদানের সামঞ্জস্য, ঘষিয়া তুলিয়া ফেলার ধরণ, গ্রিটের আকার, চাকার ধরণ, প্রয়োগ, গ্রাইন্ডারের সামঞ্জস্য, কাজের নির্দিষ্টতা, সুরক্ষা, ব্র্যান্ডের গুণমান এবং খরচ বিবেচনা করে, অপারেটররা তাদের গ্রাইন্ডিং প্রক্রিয়াগুলিতে দক্ষতা এবং সুরক্ষা বাড়ানোর জন্য সচেতন সিদ্ধান্ত নিতে পারে।
গ্রাইন্ডার এবং ডিস্কের সামঞ্জস্যের জন্য সুরক্ষা নির্দেশিকা মেনে চলা, উপযুক্ত ব্যক্তিগত সুরক্ষামূলক সরঞ্জাম পরা এবং প্রস্তুতকারকের সুপারিশ অনুসরণ করা অপরিহার্য। ভারী স্টক অপসারণ, পৃষ্ঠের সমাপ্তি, বা কাটার অ্যাপ্লিকেশন যাই হোক না কেন, সঠিক গ্রাইন্ডিং ডিস্ক কাজের গুণমান এবং দক্ষতার উপর উল্লেখযোগ্যভাবে প্রভাব ফেলতে পারে।
অতিরিক্তভাবে, ক্ষয়ক্ষতির জন্য পর্যায়ক্রমিক পরীক্ষা, অতিরিক্ত গরম এবং কম্পনের মতো সমস্যাগুলি সমাধান করা এবং লোডিং সমস্যাগুলি বোঝা গ্রাইন্ডিং ডিস্কের আয়ু দীর্ঘায়িত করতে এবং ধারাবাহিক কর্মক্ষমতা নিশ্চিত করতে অবদান রাখে।
সংক্ষেপে, গ্রাইন্ডিং ডিস্ক নির্বাচন, ব্যবহার এবং রক্ষণাবেক্ষণের জন্য একটি সু-জ্ঞাত এবং পদ্ধতিগত পদ্ধতি সর্বোত্তম ফলাফল অর্জন, উৎপাদনশীলতা বৃদ্ধি এবং একটি নিরাপদ কর্ম পরিবেশ নিশ্চিত করার মূল চাবিকাঠি।
পোস্টের সময়: জানুয়ারী-১২-২০২৪